از خاک آهن تا کیمیای نفت
حکایت بذر اعتمادی که در هوای تحریم جوانه زد
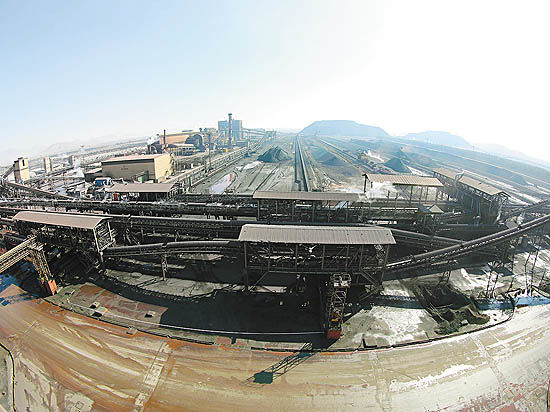
اما تولید هر یک از این آلیاژها در صنایع فولادی داستانی مجزا برای بازگو کردن دارد. نظر به رشد سریع علمی ایران و جایگاه به نسبت مطلوب کشور در تولید علم؛ بهخصوص در علوم مهندسی مثل متالورژی و همچنین تجربیات متعدد ساخت تجهیزات پیشرفته یا نیمهپیشرفته در صنایع مختلف، میتوان ادعا کرد که توان مهندسی کشور تا حدود زیادی توانایی پاسخگویی به نیازهای صنعتی متکی به تکنولوژی همانند تولید آلیاژهای فولادی مورد نیاز صنایع نفت و گاز را دارد، اما عمدتأ موانع دیگری وجود دارند که مانع استفاده حداکثری از ظرفیتها میشوند. به اذعان مدیران نفتی و فولادی کشور، یکی از این موانع نبود یکپارچگی مدیریتی در مراحل مختلف تولید است. اتفاقأ رفع همین مانع در پروژه خط لوله گوره به جاسک بود که باعث شد شرکت فولاد مبارکه به همراه شرکت فولاد اکسین و سایر کارخانههای لولهسازی بتوانند خودی نشان دهند و اثبات کنند که صنایع نفت و گاز میتوانند برای تامین نیازهای فولادی خود به داخل تکیه کنند.
در شمایی کلی، بسیاری بر این باورند که تحریمهای ظالمانه آمریکا علیه فولاد و نفت و گاز و سایر صنایع ایران بهرغم خسارتهای فراوان اقتصادی، نوعی خودباوری را در بین ما زنده کرد. البته بر اساس آمارها و نظرات مطلعان، این موضوع نیز بسان همان ماجرای مرغ و تخممرغ است و معلوم نیست که آیا نخست نطفه خودباوری در صنعت بسته شد و بعد از آن تحریمهای هستهای در نقش کاتالیزگر اتکای بیشتر به توان داخلی عمل کردند یا اینکه خود تحریمها بودند که از ابتدا بانی توجه بیشتر به تولیدکنندگان داخلی شدند. موید گزاره اول، آمار و ارقام مربوط به سرعت رشد علوم در ایران از حدود سالهای ۱۹۹۰ میلادی به این سو است. بر اساس گزارشی از مجله ساینس متریکس به نام ۳۰ سال در علم که در سال ۲۰۱۲ منتشر شد، رشد تولیدات علمی ایران بهخصوص در علوم مهندسی و ریاضیات از سالهای پایانی دهه ۸۰ میلادی سرعت گرفت و برای سالها در جایگاه نخست جهان ماند. بر اساس این گزارش، در سال ۲۰۱۰، ایران با رشد علمی ۴/ ۱۴درصدی (۱۱ برابر میانگین رشد علمی در جهان) در حالی در جایگاه نخست رشد جهان قرار داشت که کشور دوم (کره جنوبی) با اختلاف ۶/ ۴درصدی، ۸/ ۹ درصد رشد علمی را تجربه میکرد. این رشد سریع طی ۱۰ سال گذشته نیز ادامه داشته و ایران همواره جزو سه کشور نخست دنیا در رشد تولیدات علمی بوده است. همچنین بر اساس گزارشی از تهرانتایمز، ایران که در سال ۲۰۱۲ در جایگاه بیستوچهارم بیشترین تولیدکنندگان علم در دنیا بود، در سال ۲۰۱۹ به جایگاه شانزدهم ارتقا یافت. بر اساس وبسایت موسسه رتبهبندی سیماگو (scimago)، ایران در سال ۲۰۱۹ در تولید علم در رشتههای مهندسی در رتبه دوازدهم جهان قرار گرفت. این آمارها نشان میدهد که تجمیع اندوختههای ایران برای استفاده از ظرفیت بومی صنایع از مدتها قبل از وضع تحریمهای هستهای علیه صنایعش آغاز شده است.
اما گزاره دوم، یعنی اثر محدودیتهای ایجادشده در واردات تجهیزات و تکنولوژی به واسطه تحریمها بر توجه بیشتر به ظرفیت داخلی، بیش از گزاره نخست از زبان دستاندرکاران صنعت در ایران شنیده میشود. یک نمونه از آن را میتوان در رابطه نفت با صنعت فولاد دید. در حالی که صنعت نفت به عنوان بزرگترین صنعت ایران نیاز عدیدهای به انواع آلیاژهای فولادی پیچیده در اندازهها و ضخامتهای مختلف دارد و همچنین ایران از نظر منابع سنگآهن کشوری غنی به حساب میآید و حتی صنایع فولاد بزرگی هم دارد، اما به اذعان برخی مدیران اجرایی صنعت نفت تا پیش از تحریمهای هستهای که در درجه نخست صنایع نفتی ایران را نشانه گرفت، ترجیح بر استفاده از قطعات و خدمات خارجی بود و بهخصوص آنجا که بحث اعتماد به دانش فنی و تامین آلیاژهایی از فولاد که تکنولوژی خاصی را میطلبد پیش میآمد، عملأ فرصتی برای خودی نشان دادن صنایع فولادی داخلی در بازار صنعت نفت ایران دست نمیداد. محمود محمدی فشارکی، مدیر برنامهریزی کنترل تولید شرکت فولاد مبارکه به تجارت فردا گفت که «نیاز صنایع نفت و گاز به ورق فولادی برای محیطهای ترش و شیرین تا قبل از سال ۹۸ از طرف شرکتهای اروپایی و چینی تامین میشد و با توجه به تحریمهای صورتگرفته در صنعت نفت و گاز کشور بود که از این سال کنسرسیومی متشکل از وزارت نفت، فولاد مبارکه و فولاد اکسین و شرکتهای لولهساز تشکیل و بنا شد امکان تولید نیاز وزارت نفت به ورق فولادی در داخل کشور تامین شود». در همین راستا، عبدالرضا حاجیحسیننژاد، مدیرعامل سابق شرکت مهندسی و توسعه نفت به «تجارت فردا» گفت که عدم اطلاع طراحان و کارفرمایان از ظرفیت داخلی گاهی باعث نادیده گرفته شدن صنایع داخلی میشود. به گفته او، ابعاد هر پروژهای از زمان طراحی شکل میگیرد. بنابراین اگر در زمان طراحی پروژه، کارفرما و مهندسان مشاور اطلاعات کافی از امکانات ساخت داخل داشته باشند، در تعداد زیادی از پروژهها میتوانند طراحی را به گونهای انجام دهند که امکانات داخلی کشور بتواند پاسخگوی تجهیزات آنها باشد. به عنوان مثال، اگر در پروژهای پمپی در نظر گرفته شود که امکان ساختش در ایران وجود نداشته باشد، میتوان به جای آن پمپ از دو پمپ با ظرفیت کمتر ساخت داخل استفاده کرد که در داخل ایران ساخته میشوند. همین اتفاق دقیقأ در پروژه خط لوله گوره-جاسک رخ داد، اما به عقیده حسیننژاد، فشار تحریمها محرک چنین رویدادی شد و اراده داخلی برای چنین تصمیمی کمرنگ بود. به گفته این مسوول سابق نفتی، در ساخت لولههای انتقال نفت گوره-جاسک توسط شرکتهای فولاد مبارکه و فولاد اکسین نیز در واقع، تحریمها بود که روند اعتماد صنعت نفت به فولادسازان داخلی را تسهیل کرد.
اتصال حلقههای زنجیره صنعت
به هر روی، به نظر میرسد که پروژه ملی احداث خط لوله هزارکیلومتری انتقال نفت گوره-جاسک نمونهای از رشد باور نفتیها به تامینکنندگان داخلی است. بخش اصلی، یعنی تامین لولههای این پروژه با همکاری فولادیها برای تکمیل زنجیره تولید از سنگآهن تا لولههای ضد اسید و ضد شرایط سخت محقق شد. به این صورت که ابتدا سنگآهن استخراجشده در معادن ایران پس طی مراحلی در کارخانه فولاد مبارکه تبدیل به آهن اسفنجی شده و سپس وارد مرحله تولید تختال یا اسلب میشود تا خواص اولیه مورد نظر برای لولهها در تختال ایجاد شود. بنا به گفته محمدعلی توحیدی، مدیر متالورژی و روشهای تولید شرکت فولاد مبارکه لولههای به کار بردهشده در پروژه
گوره-جاسک باید مقاوم در برابر خوردگی گاز H۲S باشند. با تکنولوژیهایی مثل واحد سولفورزدایی و گاززدایی (RH) که در مجتمع فولاد مبارکه وجود دارد، میزان سولفور و هیدروژن موجود در فولاد را که باعث خوردگی فولاد میشود بهشدت پایین میآورند و با این کار درصد خلوص فولاد نسبت به این دو عنصر بالا رفته و در نتیجه مقاومت فولاد در برابر نفت و گاز ترش (با سطح گوگرد بالا) افزایش مییابد.
در مرحله بعدی، این تختالهای مخصوص به مجتمع فولاد اکسین برده شده و در آنجا فرآیند نوردکاری مخصوصی برای بالاتر بردن مقاومت در برابر خوردگی روی آنها انجام میشود. در مرحله نهایی ورقهای فولادی به کارخانههای لولهساز برای تبدیل شدن به لوله میروند تا بدینترتیب، زنجیر فولادی متصلکنندهای میان صنایع از تولیدکنندگان سنگآهن تا سازندگان لولههایی با ویژگیهای خاص برای خدمت به صنعت نفت و گاز کشور شکل بگیرد.
حلقههای مفقودهای که کمکم کشف میشوند
بهرغم تمامی آنچه گفته شد، آنچه در پروژه خط لوله گوره-جاسک میان صنایع فولادی دیده شد نمونهای منحصربهفرد از تشکیل چنین زنجیرهای از حیث اندازه و اهمیت پروژه است و هنوز تبدیل به اصل نشده. در بعد عملیاتی، سستی باور به توان داخلی بیش از هر جا در فرآیندهای مدیریتی جلوه میکند تا دانش فنی و تکنولوژی. کارفرمایان میدانند که معمولأ دانش فنی برای انجام یک پروژه یا تولید یک محصول منحصربهفرد یا وجود دارد یا قابل دستیابی است، اما همین تشکیل نشدن زنجیرههای صنعتی موجب مورد استفاده قرار نگرفتن حداکثر توان شرکتهای داخلی در پروژهها میشود. در این باره، غلامرضا سلیمی، مدیر فولادسازی و ریختهگری مداوم فولاد مبارکه قبلاً به تجارت فردا گفته بود که «باید دستاندرکاران تاثیرگذار زیر یک چتر فرماندهی واحد اقدامات صورتگرفته در حوزه معدن و فولاد را مورد بازنگری و ارزیابی قرار دهند، زیرا اگر فکری برای رشد و توسعه نامتوازن و ناهماهنگ صنعت فولاد فعلی کشور نشود، هیچ تناسبی میان حلقههای زنجیره بهرغم تلاشها ایجاد نخواهد شد. در واقع هنگامی که بدانیم جنس فولاد متاثر از بخش معدن، بخش خصوصی سرمایهگذار در آن، بخش دولتی، صنعت حملونقل، واحدهای ذوب، احیا و نورد و بازار و بورس است، لزوم وجود یک مرکز فرماندهی برای سامان دادن به اقدامات بیضابطهای که در آن انجام شده بیشازپیش پررنگ میشود.»
همین نظر را مدیران نفتی هم ابراز میکنند. عبدالرضا حاجیحسیننژاد، مدیرعامل سابق شرکت مهندسی و توسعه نفت به تجارت فردا گفت که بهترین حالت این است که مسوولیت تولید قطعات فولادی مورد نیاز وزارت نفت از مرحله تامین سنگآهن تا مرحله تولید لوله توسط یک شرکت تقبل شود تا اگر یک قطعه دچار نقص بود، مشخص باشد که مسوولیت این نقصان با چه شرکتی است.
طیف گسترده نیازهای نفتیها به فولاد
همانطور که محمدعلی عمادی، سرپرست سابق پژوهشگاه صنعت نفت به تجارت فردا گفت، فولاد در درجه استانداردهای مختلفی در صنعت نفت کاربرد دارد و با توجه به منطقه و سطح ترشی، شوری، اسیدی و پرفشار بودن مواد استخراجی یا پالایشی از آلیاژهای مختلفی استفاده میشود. به عقیده عمادی، دو عامل باعث میشود که صنعت نفت نتواند همه فولاد مورد نیاز خود را از شرکتهای داخلی تامین کند. نخست نبود تکنولوژی تولید برخی آلیاژهای خاص است. مثلاً چاههای میدان گازی پارس جنوبی اسیدیته و ترشی بسیار بالایی دارند و لولههای مورد استفاده در آنها باید از درجه استاندارد CRA باشند که تکنولوژی تولید آن در ایران وجود ندارد. عامل دوم مقرونبهصرفه نبودن تولید برخی آلیاژهای خاص با وجود توان تکنولوژیکی تولیدشان یا نبود ظرفیت کافی تولید در داخل است. به عنوان مثال برای صادرات گاز به عراق، ورق فولادی مورد استفاده برای خط لوله از هند تامین و توسط شرکتهای ایرانی تبدیل به لوله میشد، زیرا تولیدکنندگان ایرانی ظرفیت تولید ورقهای فولادی مورد نیاز برای آن پروژه را نداشتند. در رابطه با تنوع نیازهای صنعت نفت به فولاد، عبدالرضا حاجیحسیننژاد، مدیرعامل سابق شرکت مهندسی و توسعه نفت نیز بیان کرد که «معمولاً مجری پروژهها وقتی میخواهند خرید کنند، از جایی خرید میکنند که همه نیازها را بتواند تامین کند. مثلاً اگر مجری ساخت پالایشگاه بخواهد لوله خریداری کند، آلیاژهای مختلف با سایز و ضخامتهای مختلفی را نیاز دارد و ترجیح میدهد از لولهسازی خرید کند که همه این انواع را داشته باشد». به عنوان نمونه، پروژه خط لوله گوره-جاسک از نظر ابعاد تختالهای مورد نیاز تنوع بالایی دارد که ضخامتهایی از ۱۴ میلی متر تا ۲۱ میلیمتر را دربر میگیرد. به گفته محمدعلی توحیدی، مدیر متالورژی و روشهای تولید شرکت فولاد مبارکه طراحی هر یک از این ابعاد از نظر آنالیز شیمیایی و خواصی که باید داشته باشند، پروژهای مجزا با تمام پیچیدگیهایش به حساب میآید. با تمام این اوصاف، تامین نیازهای فولادی صنعت نفت از داخل تنها به تامین لولههای ضد اسید و ضد شرایط سخت خلاصه نمیشود. بلکه اکثر لولههای خطوط انتقال نفت و گاز شیرین و فرآوردههایی که خورندگی بالایی ندارند توسط سازندگان داخلی در حال تامین شدن است. به عنوان مثال در یک سال اخیر، شرکت فولاد مبارکه علاوه بر تولید ۴۵۰ هزار تن تختال برای پروژه گوره-جاسک، ۲۵۰ هزار تن تختال گاز شیرین نیز تولید کرد. این اعداد و ارقام نشان میدهد که در مجموع حدود ۱۰ درصد از ظرفیت تولید فولاد مبارکه در اختیار صنعت نفت و گاز کشور قرار گرفته است.